Corporate
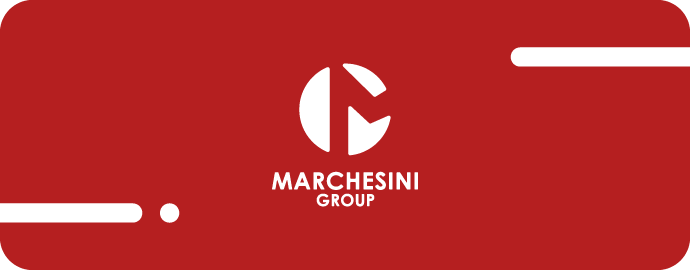
The showcased technology at the upcoming Marchesini Group Beauty Open House (15 and 16 March) will be a large line for skin care products sold to a French CDMO, used for filling and packaging botulin in syringes placed inside paper trays, a special feature which provides the line with an important added benefit in terms of product sustainability.
Various Marchesini Group brands contributed to the line’s realisation. The Corima division - which in recent years has supported a large number of pharmaceutical companies with technologies for packaging Covid vaccines in syringes and vials - supplied the two machines used upstream for the syringe de-nesting, assembly and labelling procedures.
The heart of the machine is its robotic island comprising three Pick & Place arms - all created on-site - for the high-speed feeding and handling of delicate, fragile syringes. The first robot manipulates the syringes and needles supplied by a plate elevator constructed by the Tonazzi-Vasquali division.
The needles are placed on a specific belt which conveys them to a wheel which, in turn, transfers them to the conveyor system of the robotic island. They will then be placed in the paper tray by the second robot and transferred to the chain of the cartoner by the third robot.
The most important feature of this solution is the fact that the thermoforming machine - normally used on a line to create from a PVC reel, and seal, the plastic trays that accommodate the syringes - is eliminated and replaced by a robotic island, which places the syringes in cardboard trays, subsequently packed in a carton by a cartoner.
This alternative approach to syringe packaging has multiple benefits: it is more eco-sustainable since it uses cardboard instead of plastic packaging, and production costs are lower since syringes no longer have to pass through a thermoforming process. This line thus provides greater environment-friendliness combined with across-the-board savings thanks to a technology well tried and tested on the Pharma product market, which is now also made available, with the necessary adaptations, for the Beauty product sector.
Once filled, the carton moves on to an automatic labelling machine from the Neri Division, which labels and serialises it. The ability to install all the main traceability devices available on the market – such as Laser or Ink-Jet printers – makes this machine a complete, easy-to-use and versatile solution that can meet any kind of production requirement related to pharmaceutical traceability.
The line is completed by a casepacker-palletiser with a robotic arm – the fourth installed on the line – constructed in anodised aluminium plates to increase the structure’s strength and rigidity during carton picking and placing.
Quality control on all components during packaging is entrusted to the vision systems produced by SEA Vision: installed right along the length of the line, they verify the presence, correctness and quality of every single component included in the pack.
From the line’s very first phase, the systems verify the variable data and codes printed on the syringe and needle labels by means of the Software Databox and check that labels are correctly applied to the syringe themselves by means of precise skew control.
Inspections continue on the robotic island: here the system precisely verifies the presence of all tray components and the correctness of all codes and characters printed on leaflets, instruction booklets and cartons. The end result is thus a line that guarantees the highest quality standards necessary in the pharmaceutical industry.