Corporate
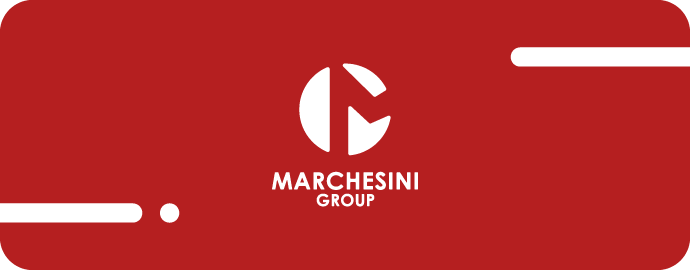
We recently delivered a new high-speed line for aseptic filling of pre-filled syringes and ready-to-use vials to a major German pharma multinational’s Latina plant.
The project took place over an extremely short timeframe, just six months: the order, booked in January 2021, was followed by the assembly of the line, composed of five machines, and its installation in a 1,000-square-metre sterile industrial environment in July of the same year. The exceptionally fast turnaround was due to a special partnership between Marchesini Group and the customer in order to meet the need to accelerate projects relating to technologies involved in the packaging of biologics.
The pandemic also influenced the decision to choose a dual format: this means the customer has a fill-and-finish line for biologics which is able to swiftly adapt to market requirements, providing impressive production rates of 36,000 syringes and 15,000 vials per hour.
This line is the first step in the customer’s strategy which aims to expand the areas dedicated to sterile filling technology in its Latina plant, where every year 80 million ampoules and over 180 million pre-filled syringes containing biologics are produced.
The high-speed line for filling of pre-filled syringes and ready-to-use vials was produced by Corima Division, the Marchesini Group brand specialised in sterile-environment packaging technology, required for processing of pharmaceuticals such as vaccines and cancer drugs.
The production process has been entrusted entirely to some of Corima’s most tried and tested solutions, in particular:
Freetub 10-A, a machine for cutting and removing the bag containing the syringe tub or the vial tray.
Freetub 20-A, a machine for opening the syringe tub and vial tray.
Extrafill 10: the heart of the line is composed of this linear filling machine responsible for the denesting, filling and capping of syringes or vials Extrafill 10 offers at least four major benefits:
The next solution, Nextra N15, handles renesting of the syringes, which then continue towards an inspection machine. A second robot, installed inside the Nextra N15, manages renesting of the syringes with no glass-to-glass contact in order to preserve their integrity.
The vials are finally send to the Capsy-LC for capping and final closing. Capsy, the perfectly balanced combination of high-technology and Italian design, is a machine which not only complies with all requirements imposed by regulatory bodies for injectable products, but is also able to carry out washing, drying and decontamination in half the time taken by traditional machines.